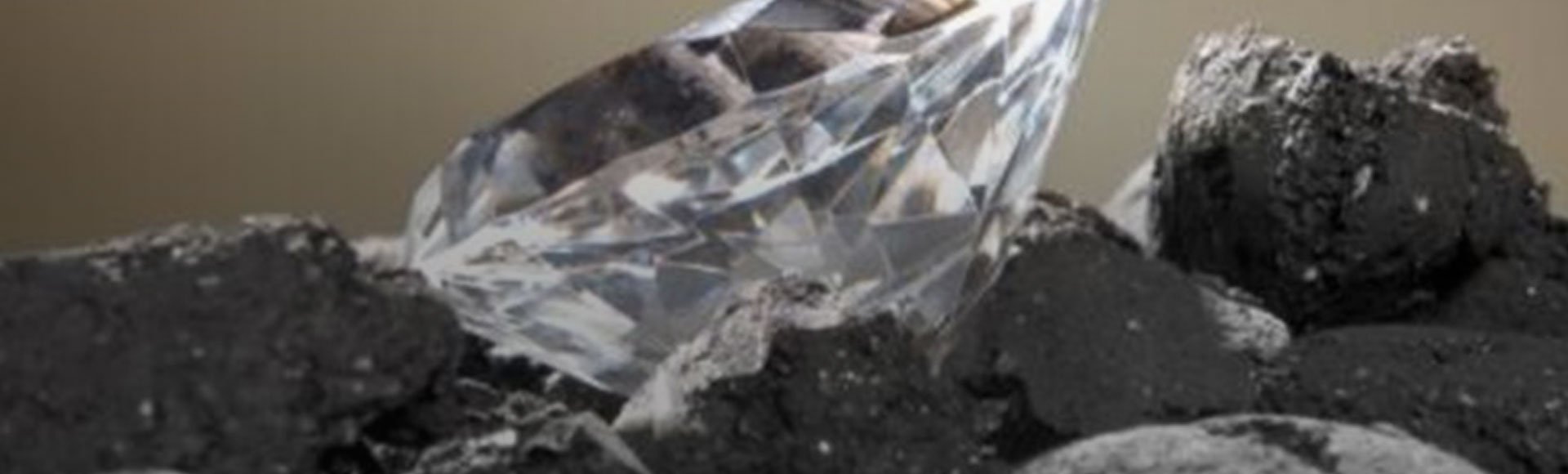
Underground mine scheduling
Making evidence-based decisions on automation options to make the best use of CAPEX investments
Confidential mining client
|
2020
Maximize throughput.
Faster decision making.
Avoid costly assumptions.
Challenges
- The client was investigating the impact of different automation options on throughput and crew utilization and wanted to use data to justify and drive investment decisions in its autonomous mining strategy across its network of underground mines.
- The client had specific constraints such as short-term sequencing of mining tasks, dependent on mining phase, crew requirement per task, and optimal crew allocation; ore storage capacity at bins and different routing of the ore to each bin; limited conveyance capacity and limited hoist capacity; and planned maintenance activities and timing of off-shift time, such as lengthy shift changes and lunch breaks.
- Engaged by the client to review their approach, assess different automation options, and make recommendations.
Solutions
- Configured a detailed scheduling model using the Hatch Optimizer to streamline the decision-making process.
- Evaluated automation options for underground mine operations and quantified the impact on the overall production and crew utilization.
- As a result, the client was able to understand maximum throughput for the mine’s current state of automation and for different automation options; identify the best operation strategy under future automation options; avoid costly assumptions by detailed optimization of operations under each scenario; and understand the impact of automation on operation sequencing and workforce utilization for different automation options, as well as uncover new bottlenecks in the system.
Highlights
- Efficient determination of optimal operation for each automation option—getting the best solution the first time.
- Maximized the overall production throughput under a new operation environment.
- Identified the best operation pattern and crew allocation for each automation option.
- Identified system bottlenecks and the best way to work around them through a holistic, simultaneous optimization of production and conveyance.
- Simultaneously incorporated production potential, equipment capacities, and crew constraints such as manpower required to perform tasks, shift changes, and lunch breaks.
Project numbers
Approx 10% tonnage improvement opportunity identified
10-20% productivity improvement opportunity identified