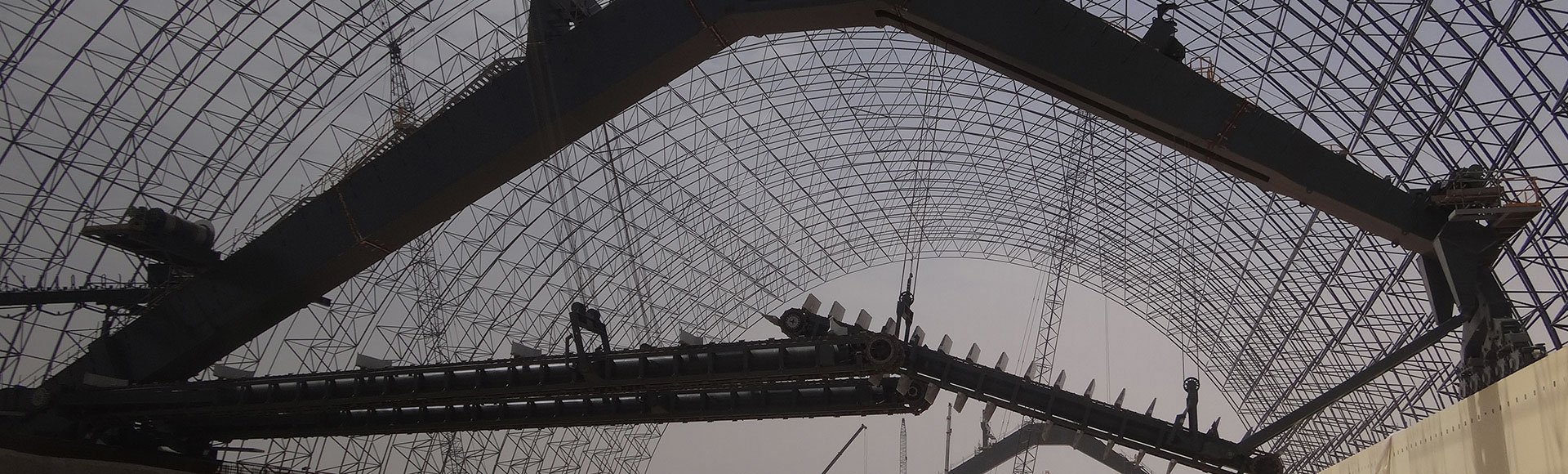
Habshan Sulfur Granulation
Engineering one of the largest sulphur-granulation installations in the world
GASCO
|
United Arab Emirates
|
2011–2013
180,00-tonne covered-storage stockpile.
11,000-tonne-per-day sulfur-granulation plant.
75-km pipeline.
Challenges
- GASCO set out to build the largest integrated gas-to-liquids refinery in the world.
- Liquid sulfur would arrive from existing Habshan gas plants via skin-effect electrical tracing (SEET) pipelines.
- The liquid sulfur would then be granulated at the facility, stockpiled, and ultimately transported via rail to a new sulfur handling terminal at Ruwais.
- The right measurements were required to effectively handle the friable sulfur granules and mitigate concerns surrounding fire hazards.
Solutions
- Provided detailed engineering and procurement support services for the upstream liquid-sulfur delivery pipeline and the downstream bulk-material-handling facility.
- Included two stacker-reclaimers in the bulk-material-handling system that were integrated within a conveyor network that then connected to a railcar-loading facility.
Highlights
- The materials-handling system used many automation strategies to ensure the designed "hot-spare" redundancy provisions were effective.
- Developed a custom stockpile-management philosophy to eliminate shelf-life issues for sulfur kept in storage.
- With 12 granulators and an extensive network of sulfur pipelines, this is one of the largest sulfur granulation installations in the world.
Project numbers
7 conveyors1,000-tonne surge bin
4,000-tonne per hour rail-car-loadout facility
5 wet-dust-collection-scrubber towers