RAM Simulation: A Model Approach for Optimizing Assets
Since the mid-1980s, we have helped clients by effectively combining process and operational understanding, engineering know-how, modeling and simulation expertise to develop RAM models.
RAM modeling is a powerful tool that can optimize facility design through the effective integration of equipment, within overall system design, from initial conceptual flow scheme development, through to ongoing operations and maintenance. It can accurately quantify expected plant production, identify, and avoid bottlenecks and downtime, increase operational capacity, and eliminate unnecessary capital investments.
RAM simulation to predict and track the performance of assets can be applied in numerous sectors, including mining, energy, and infrastructure. Its data-driven approach produces a probabilistic, logic-based consequence model that can:
- Identify “bad actors” that contribute to unplanned downtime, on an equipment level
- Highlight the contribution of the major units of operations (and sub-units as applicable) to overall plant unavailability
- Fine-tune buffer capacities and test utility buffer impacts on plant availability
- Help verify and evaluate storage requirements to design sufficient storage capacity for product loading and dispatch of products
- Optimize maintenance shutdown duration and accelerate maintenance planning early on in the design phase
- Provide input to sparing philosophy (e.g., plan for spare parts and equipment in the event the system fails)
- Plan for equipment isolation philosophy (e.g., method for isolating a section in the facility to allow safe operation while maintenance or inspections are carried out)
- Develop production histograms for production planning
- Aid in emissions estimates
- Promote efficiency and profitability
- Identify the impacts of interferences or variations upstream or downstream of the facility boundaries
The overall performance and life cycle of any asset is dependent on numerous variables such as physical equipment characteristics, production process parameters, and maintenance practices. To effectively account for this complexity, the earlier RAM modeling is introduced, the better. The following graph shows how the RAM process can help discover reliability issues early in the design process, when they can be corrected in the most cost-effective manner.
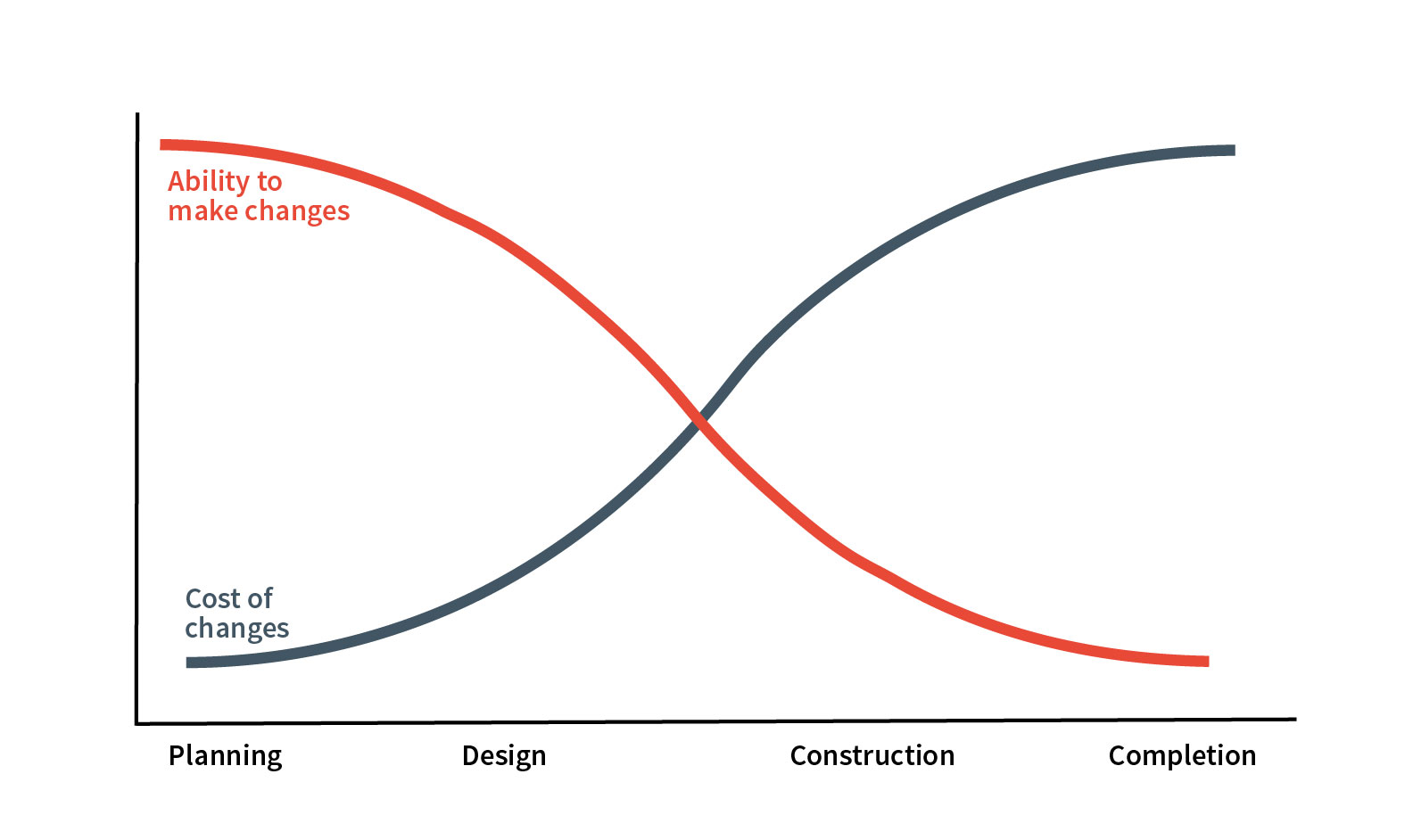
Hatch has a proven track record of delivering both static and dynamic RAM modeling outcomes for asset optimization.
Static RAM modeling is an effective tool in identifying and pinpointing where issues are likely to arise in a facility, especially during early design phases when process dynamics are not yet completely defined but major process units and equipment have been identified. We typically develop the RAM model within the Availability Workbench (AWB) software platform and report the overall projected facility availability, the contribution of specific equipment to unavailability, and the expected annual throughput, relative to a steady state mass balance (e.g., no variability in feed or end-product compositions). Both high level process logic and equipment failure attributes are key determinants in equipment and system downtime calculations. The Static RAM model is developed based on the Monte Carlo Approach, which relies on repeated random sampling to measure variations, using inputs such as failure characteristics, maintenance strategy, and operating logic. This is combined with industrial statistics and experience derived from similar applications.
Dynamic RAM simulation is a differentiated service offered by Hatch. In system design, process variability is a common source of real-world complexity and with dynamic simulation these variations can be accounted for and quantified. This approach incorporates equipment capacity, availability, and reliability with various aspects of plant design and operation. These aspects include input feed, end-product compositions, buffer times, upstream or downstream disturbances, and equipment failures.
Our team is regarded as a super user of the Arena simulation software platform, which features animation that allows for the visualization of a system’s performance. To improve the efficiency and veracity of the simulation process, we have created and implemented various supplemental in-house tools, including an Excel-based model interface to simplify case execution and to improve report generation.
We have successfully applied RAM modeling to numerous projects, including XTL technology, blue hydrogen flow scheme development, and testing of an oil shale processing facility.
A recent example of our work involved an XTL project on the Louisiana Green Fuels Project for Strategic Biofuels’ biomass to liquids project in Louisiana, USA. The initial static RAM model developed for the project during the early engineering design phase, served to highlight the impact of shutdown durations and the key role of the process buffers in safeguarding plant availability. The subsequent dynamic RAM model further advanced the understanding of how preliminary maintenance and shutdown philosophies could be optimized, and the importance of robust design of utility provision units (e.g., power, water, steam etc.) to overall plant availability. The reliability analysis also served as a data driven basis for the development of an appropriate sparing philosophy to enable effective preventative maintenance strategies.
Our goal on all of our projects is to provide innovative, cost-effective, efficient solutions that enhance reliability, availability, and maintainability of the anticipated facilities. Our expertise, experience, and proven methodology combine to generate highly efficient solutions in a cost-effective way.
At Hatch, we take a model approach to RAM simulation, which in turn, provides our clients with a model for success.
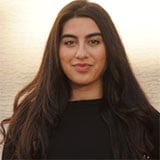
Diana Haikal
Process Engineer in Training, Oil & Gas
Diana is a process engineer in the Hatch Oil & Gas business unit with a B.Sc. degree in Chemical Engineering from the University of Calgary. Her passions include RAM analysis, and CCS technologies. In her free time, she is outdoors enjoying what nature has to offer.