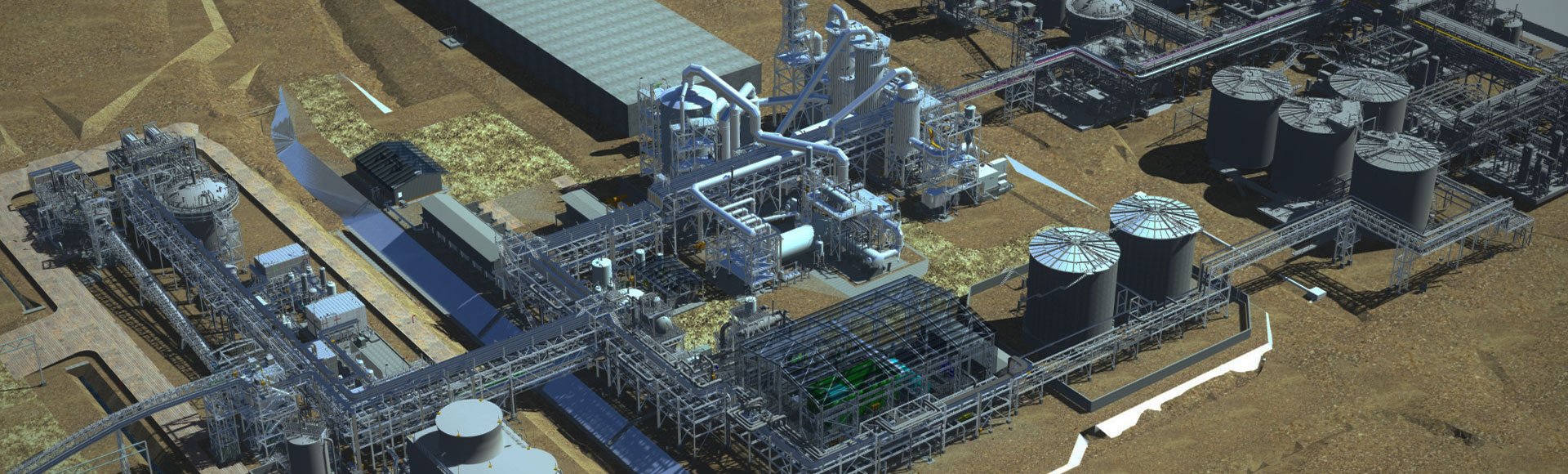
Planta de Ácido Sulfúrico
República Democrática del Congo (RDC)
|
El proyecto recibió el Premio Year in Infrastructure de Bentley Systems.
Instalación de fabricación de 1 400 toneladas por día.
Éxito en la ejecución de la planta en menos de dos años
Desafíos
- Elegidos como el contratista de ingeniería, adquisiciones y administración de la construcción para una nueva planta de fabricación de ácido sulfúrico en una remota provincia al sur de la República Democrática del Congo.
- Se decidió no producir los planos tradicionales de mecánica, tuberías o la distribución estructural general, y en su lugar se usó un modelo en vivo para todas las necesidades de producción.
- Los procesos de calidad de ingeniería se implementaron desde el inicio mediante el modelado en 3D, lo que permitió comprimir los plazos del proyecto de un modo que hubiera sido imposible utilizando los tradicionales procesos de calidad isométricos de tuberías basados en planos.
- Se superaron los desafíos geográficos y logísticos, y se logró entregar una planta en menos de dos años, desde la etapa de viabilidad hasta la puesta en marcha.
Soluciones
- Se logró entregar una nueva planta de fabricación de ácido sulfúrico en la RDC en menos de dos años, desde la viabilidad hasta la puesta en marcha.
- Se diseñó un gemelo digital completo e inteligente a fin de administrar y compartir información entre sus oficinas de ingeniería en Canadá, Sudáfrica, India, Australia y la RDC.
- En lugar de producir planos tradicionales, el equipo del proyecto utilizó el modelo en vivo para todas las necesidades de producción.
- El enfoque de gemelo digital en todo el proyecto permitió eliminar los flujos de trabajo tradicionales en papel y maximizar las oportunidades de adquisiciones centradas en datos, acelerar la preparación operativa y mejorar la interacción con las actividades en terreno en una ubicación remota.
- El enfoque permitió finalizar varios meses antes de lo previsto en la programación, aumentó significativamente el retorno de la inversión al reducir los riesgos CAPEX en un 20 %, permitió empezar la producción antes y llevó la planta a su capacidad de producción plena una semana después de la puesta en marcha en caliente, lo cual no tiene precedentes en esta industria.
Puntos destacados
- Debido a los grandes riesgos ambientales de transportar ácido a esta área remota y las limitaciones en el suministro, el cliente aceleró el cronograma del proyecto.
- Los productos entregables isométricos de las tuberías se fabricaron en una progresión continua e ininterrumpida, con equipos en tres zonas horarias diferentes.
- El equipo distribuido del proyecto pudo elegir entre varias alternativas de adquisición, lo cual les permitió bajar los costos del suministro de material y simplificar la ejecución, y así reducir los plazos por meses.
Números del proyecto
Costo del proyecto: USD 245 millones.Instalación de fabricación de 1 400 toneladas por día
Un sistema de generación de energía eléctrica a partir de calor residual de20 megavatios con una torre de refrigeración térmica.
Aumento del retorno de la inversión en un 20 % al reducir los riesgos CAPEX.
10 % a 15 % de ahorros de costos para el cliente en pedidos directos de material.
Todos los materiales debían transportarse 2 800 km sobre caminos con tramos de grava.
Al contar con procesos de calidad presentes desde el origen se pudo finalizar tres meses antes de lo previsto en la programación.
Reducción del aumento de la producción de seis meses a una semana tras completar la puesta en marcha en caliente.
Servicios y tecnologías proporcionados
Haga clic aquí para ver un video del perfil del proyecto de los Premios Year in Infrastructure de Bentley.
Cómo podemos ayudarlo
Si tiene un problema que necesita ser resuelto, póngase en contacto con nosotros.