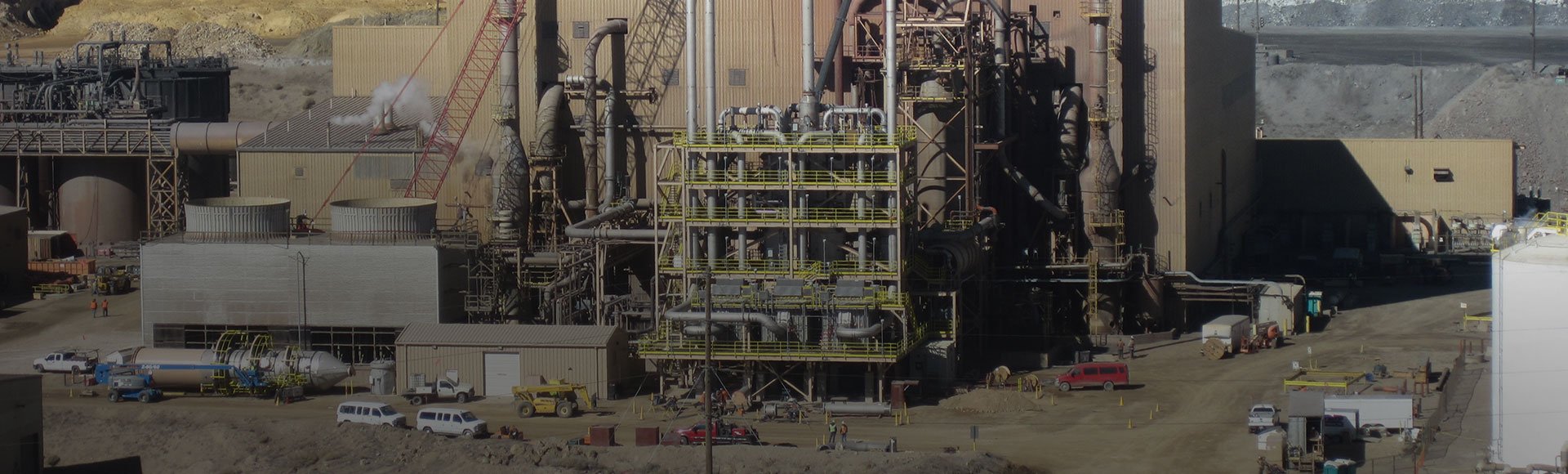
Twin Creeks Mercury Abatement project
Pre-feasibility, Feasibility, Construction & Commissioning
Newmont Mining Corporation
|
Nevada, USA
|
March 2010 – August 2013
Hg abatement system implemented with proven 99.9% removal efficiency.
Project approved as MACT by the NDEP and EPA.
70 tie-ins to existing plant all coordinated during regular annual downs.
Project completed on schedule and on budget.
Challenges
- Newmont Mining Corporation’s Twin Creeks facility is an operational refractory gold pressure oxidation facility located in Nevada, USA.
- New environmental regulations by the Nevada Division of Environmental Protection (NDEP) and the Environmental Protection Agency (EPA), required implementation of mercury abatement controls to treat the autoclave off-gas at the Twin Creeks facility.
Solutions
- Newmont Mining Corporation approached Hatch’s High-Pressure Metallurgy (HPM) practice to study mercury abatement technology options for treating the autoclave off-gas at the Twin Creeks facility.
- The project required several trade-off studies to compare commercially available mercury control technologies as well as studies to evaluate the gas conditioning options upstream of the mercury control equipment. Final design included considerations to minimize plant interruptions and provide maximum operational flexibility.
- The final process design utilizes direct gas cooling and condensing equipment to dry the gas prior to entering carbon beds for mercury adsorption. Other project requirements included a water treatment circuit for treating residual cyanide in reclaimed decant water, such that it could be used for gas quenching.
- The final design was reviewed by the NDEP and EPA and approved as Maximum Achievable Control Technology (MACT).
Highlights
- The autoclave off-gas mercury abatement system was successfully constructed and commissioned, on time and on budget, with proven 99.9% removal of the mercury.
- Successfully constructed and commissioned the water treatment plant and achieved target residual cyanide levels of <0.5 ppm.
- This was a brownfield engineering and construction project, which required demolition of existing infrastructure, relocation of buried services and effective design and scheduling of tie-ins to the operating facility.
- Execution of the project included more than 70 piping, mechanical and electrical tie-ins to the existing plant. Final tie-ins were completed within a 16-day scheduled annual shut-down and ramp-up to full production was achieved within 1 week.
- Completed project on schedule and on budget.