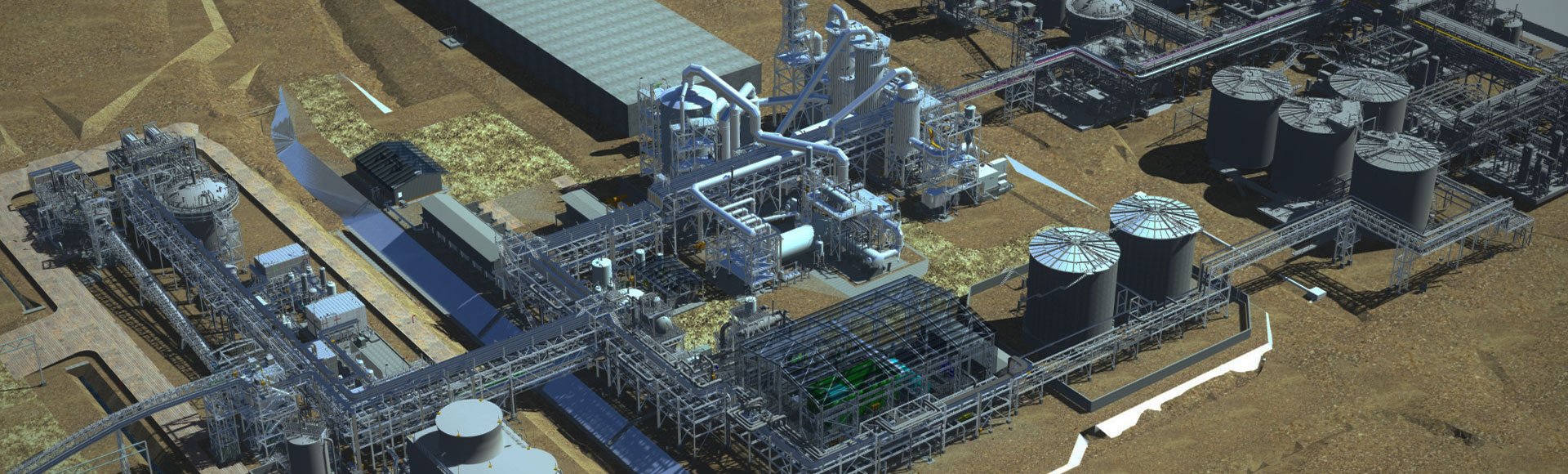
Sulfuric Acid Plant
Democratic Republic of the Congo (DRC)
|
Recognized with Bentley Systems' Year in Infrastructure Award.
1,400-tonnes-per-day manufacturing facility.
Succeeded in delivering the plant in under two years.
Challenges
- Retained as the engineering, procurement, and construction management (EPCM) contractor for a new sulfuric acid manufacturing plant in a remote southern province of the DRC.
- Decided not to produce traditional mechanical, piping, or structural general arrangement drawings and instead use the live model for all production needs.
- Moved engineering quality processed upstream using 3D modeling, enabling them to compress project timelines that would otherwise not have been possible using traditional drawing-based piping isometric quality processes.
- Overcame geographical and logistical challenges to succeed in delivering the plant in under two years, from feasibility to start-up.
Solutions
- Succeeded in delivering a new sulfuric acid manufacturing plant in the DRC in under two years, from feasibility to start-up.
- Designed a complete, intelligent digital twin to manage and share information among its engineering offices in Canada, South Africa, India, Australia, and the DRC.
- Instead of producing traditional drawings, the project team used the live model for all production needs.
- The digital twin approach across the entire project enabled the elimination of traditional paper workflows and maximized opportunities in data-centric procurement, sped up operational readiness, and improved the interaction with field activities in a remote location.
Highlights
- Given the high environmental risks of hauling acid to this remote area and constraints on supply, the client fast-tracked the project timeline.
- Produced piping isometric deliverables in a continuous "follow-the-sun" progression with teams across three time zones.
- Enabled the distributed project team to choose from multiple procurement alternatives and allowed them to lower the cost of material supply and to streamline delivery, cutting months off the schedule.
- Significantly increased return of investment by 20% by reducing CAPEX risks, enabling earlier production and getting the plant to full production capacity within one week of hot commissioning, which is unprecedented in the industry.
Project numbers
US$245 million project cost1,400-tonnes-per-day manufacturing facility
20-megawatt electrical waste heat power generation system with a thermal cooling tower
20% increase in return of investment by reducing CAPEX risks.
10% to 15% cost savings to the client in direct material requisitions
2,800-km-long transport of all materials on roads with sections that are gravel
3 months saved on schedule by moving the quality processes upstream
6 months reduced to 1 week of production ramp-up after completion of hot commissioning
Click here to watch a video profile of the project from Bentley's Year in Infrastructure Awards.