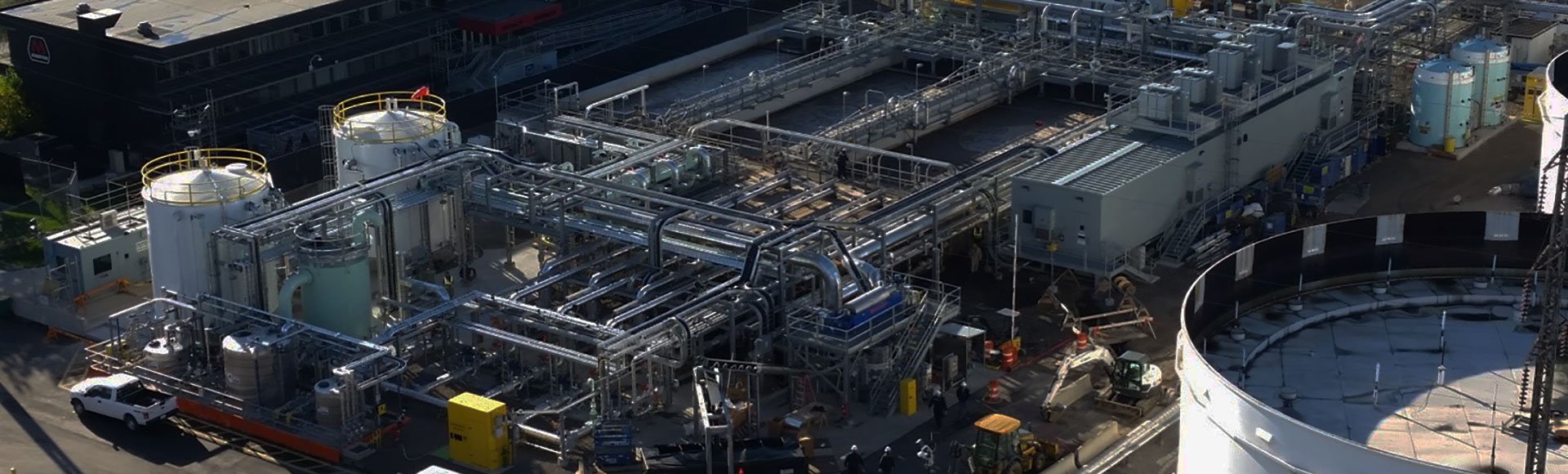
Water Outfall Project—MBR System
Using a membrane bioreactor process to meet EPA regulations
Marathon Petroleum
|
United States
|
2011-2014
First-of-a-kind technology by a North American refinery
30% less space required for membrane bioreactor system
400 piping isometrics created
High-quality effluent reused in the refinery
Challenges
- The Marathon Petroleum Company's refinery in Detroit, Michigan, has a pretreatment facility for desalter underflow water. It consists of an API separator, flocculating reactors, and clarifiers.
- In 2011, the Environmental Protection Agency released new limits for volatile organic compounds and benzene levels, which Marathon's Detroit refinery did not meet.
- Marathon Petroleum needed a partner to help develop a final solution to ensure benzene content in the refinery's wastewater outfall would be reduced to "non-detect" levels.
Solutions
- As an interim measure, a temporary hydrogen peroxide treatment system and a four-vessel granular-activated carbon system were installed. These were later upgraded to improve reliability and increase capacity.
- After a thorough evaluation of technology solutions to the problem, Hatch selected a new biological treatment system centered on a membrane bioreactor (MBR) process to replace the current interim benzene-removal process.
- We provided engineering, procurement, and construction support services. A total of 55 purchase orders were issued.
- Intelligent 3D modeling was used and over 400 piping isometrics were created. These were used for offsite prefabrication, which helped advance the construction schedule.
Highlights
- The MBR system requires approximately 30 percent less real estate, making it an effective alternative to conventional biological treatments that require more space. The system was ultimately installed in the parking lot of the engineering building.
- The effluent quality will be sufficient to allow direct reuse to occur. Additional treatment will be needed for all reuse where sensitive water-quality issues are critical, such as for boiler feed water.
- This MBR installation was the first of its kind to be used on a refinery effluent in North America.
- The system was installed on time and budget, and has been successfully producing high-quality effluent since 2014. Water reuse for boiler feed is planned for design/installation in 2019.
Project numbers
2,000 gallons per minute (gpm) average design flow3,200 gpm peak design flow