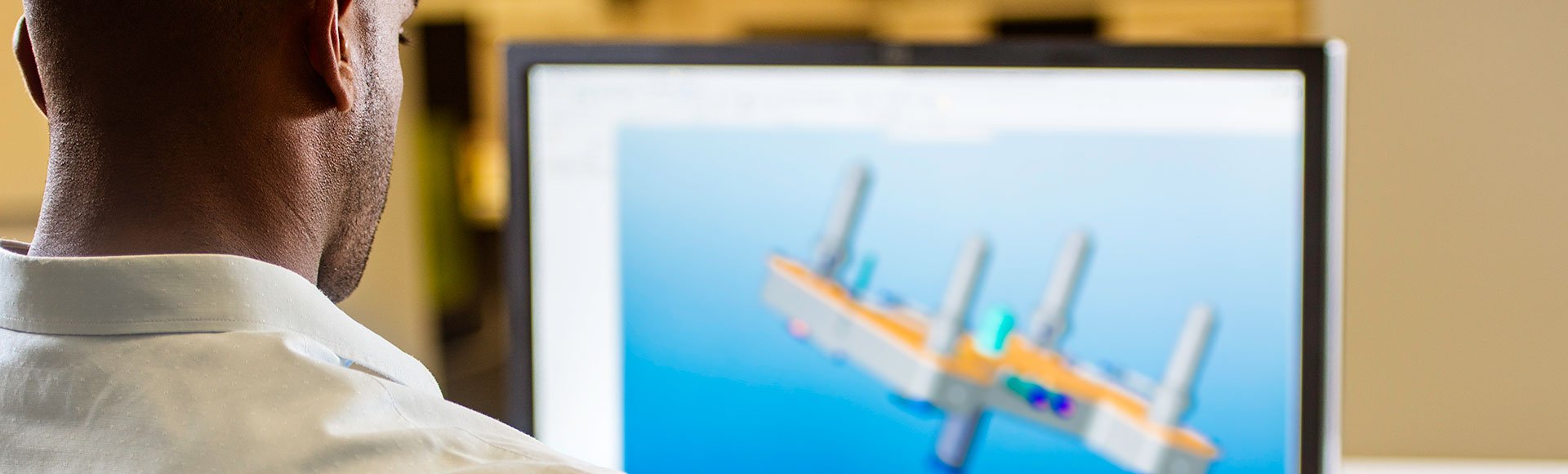
SunCoke South Shore Project
Producing more coke with clean, green energy as a byproduct
SunCoke Energy
|
United States
|
2012–2015
60,000 households powered.
1.3 million tons of iron created annually.
US$450 million project.
Challenges
- Design a greenfield metallurgical coke-making facility complete with a power island for SunCoke Energy.
- Meet strict environmental regulations while maximizing coke production and improving economics through the generation of electricity from waste heat.
- Develop an optimized plant layout within the small available footprint.
- Reduce project costs in the midst of a volatile global market.
Solutions
- Worked closely with SunCoke to develop an integrated plant design that maximizes production of its main saleable product while generating a consistent revenue stream from electricity generation.
- Leveraged a stream of generated energy that was not being used to produce revenue. Identified grid interconnection options across state lines and developed a power island to produce clean electricity to sell to the grid.
- To maximize the plant's availability, designed the system to be equipped with redundancy. Included three 50% heat-recovery steam generators and a flue gas system, allowing online maintenance of all downstream equipment.
- Designed the downstream flue-gas cleaning system with circulating dry scrubbers (2 x 100%) to minimize environmental emissions. Also assessed the overall impact to the plant water balance to reduce plant discharge.
Highlights
- Optimized the plant footprint to save costs.
- Developed a new damper design and configuration for hot gas ductwork.
- Developed a material handling layout for efficient coal handling and sampling.
- Minimized plant emissions stipulated by US EPA MACT standards.
“Hatch has a high degree of customer satisfaction at all levels of SunCoke; Hatch continues to work and provide ideas across the board with B.D. Engineering & Projects and senior management, presenting several strategic ideas for SunCoke’s business. Each level of Hatch’s team presents strong management skills.”
Project numbers
120 coke ovens660,000 tons per annum of metallurgical coke produced
3 x 50% heat-recovery steam generators and one steam turbine
82 MW of electricity produced to sell to the grid
700,000 lb/hr of flue gas at 2,200°F and producing 1,200 psig steam at 930°F—enough coke to make about 1.3 million tons of iron annually. (The entire Golden Gate Bridge weighs less than 900,000 tons.)