Modernizing port container terminals: Navigating the path to automation
Ports are crucial to global trade and international commerce, supporting a global industry worth a staggering US$14 trillion. According to the International Chamber of Shipping, 11 billion tons of goods—from raw materials to fine art and everything in between—are shipped annually. The containerized segment of the market increased by 43 percent in the last decade to 866 million twenty-foot equivalent units (TEU) in 2022—and with stress factors such as limited space for expansion, the ever-growing pace of goods exchange, shifting manufacturing centers, climate change, and geopolitical uncertainty—terminals need to be able to handle more cargo and be more agile and nimble than ever.
While terminals operators generally want to improve efficiency, productivity, safety, and return on investment, they aren’t always quick to implement new technology into their operations.
There are good reasons for this “if it ain’t broke, don’t fix it” mentality. Among them:
![]() Cost |
Implementing change, including modernization and automation, often involves significant upfront costs. |
![]() Complexity |
Complex systems can mean complex implementation. Solutions may require skilled project teams that deliver organizational change, not just procurement of new pieces of equipment. |
![]() Risk |
Large change/small time frame. Potential disruptions can affect the flow of goods, and automation can bring and increase dependence on system functionality. |
![]() Time-proven methods |
Established practices and procedures are ingrained in the culture and operations of the terminals. |
![]() Business case |
Although modernization is an enabler for many key objectives in a terminal such as improved safety, enabling energy efficiency initiatives, and reduction in costs, quantification of expected benefits can be challenging. |
![]() Labor considerations |
Modernization may lead to concerns from the workforce and unions about potential impacts on their careers and livelihoods. It's important to engage in open dialogue to address these concerns and work toward mutually beneficial solutions. |
All these concerns are legitimate. Before making any changes, container terminal operators should ask one important question: Why should they?
Modernization and automation should stem from clear objectives rather than succumbing to the bandwagon effect—doing something because everyone else is doing it. Terminal operators must meticulously assess their goals, whether it’s enhancing cargo tracking through optical character recognition (OCR) or optimizing loading and unloading processes with automated container handling equipment.
Each investment should be justified by tangible improvements in operations. Reasons for embracing automation span the spectrum, from streamlining the asset conversion cycle to enhancing safety standards, improving client service levels, and reducing production costs. Moreover, successful automation can inject flexibility, scalability, and competitive advantage into terminal operations, fostering resilience in the face of evolving industry dynamics.
Among the “whys” for modernizing and automating are:
- Cost-benefit factors: While the initial costs may be substantial, they can often be justified through increased efficiency, 24/7 productivity, faster turnaround times, and future compatibility of technology initiatives.
- Resource optimization: System enhancements can reduce the cost of production, minimize idle time, and maximize equipment utilization, thus ensuring long-term sustainability and operational continuity.
- Safety and risk management: Strict safety protocols required for automated systems and the reduction of direct exposure to operating equipment help minimize workplace accidents from high-risk tasks such as stacking containers and heavy lifting.
- Tracking and inventory: Increased accuracy enhances the overall supply change by minimizing discrepancies and reducing the risk of unaccounted for, or misplaced containers.
- Manageability: As terminals increase in size, densify and become more complex, more advanced systems are required to manage the cargo effectively.
- Reduction of emissions: Although some forms of electrification require minimal automation, the inclusion of automation and control technologies in the electrification technology suite can help to manage and optimize the new equipment, including charging infrastructure and integration with microgrids or e-grids.
- Maintenance costs: “Smart” systems and equipment are often inspected at specific and/or required intervals, which catches potential issues before they occur, resulting in lower maintenance costs.
- Competitive advantages: Updating operations and equipment can give port terminals an edge in the global marketplace through enhanced services for clients and other stakeholders.
Once port container operators figure out the “why” by comparing the advantages and disadvantages of modernizing, they must ask themselves another important question: How will they do it?
Engaging an experienced partner is a good start. Hatch has decades of experience updating and upscaling operations in the infrastructure, metals and minerals, and energy sectors.
Our experts bring a wealth of knowledge and expertise to the table, offering strategies to navigate the complexities of embracing operational change. Of course, each industry has unique issues and what works for one won’t necessarily work for another. That’s why we embrace adaptation over blind adoption. Our Hatch team combines container terminal operations experience with best practices from other industries to help clients realize their goals.
By leveraging lessons learned from past projects, we can help clients sidestep common pitfalls and accelerate their journey toward positive change.
The modernization and automation of port container terminals involves strategic foresight and human-centric considerations. By embarking on the journey with the guidance of a seasoned partner, container terminal operators can unlock new frontiers of efficiency, safety, and profitability in the ever-evolving landscape of global trade.
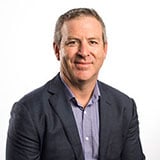
Michael Houen
Director, Smart Ports, Ports & Terminals
Michael is a maritime terminal automation expert with extensive experience in both greenfield and brownfield projects. He excels in managing complex automation projects from design to operation, enhancing process improvement, efficiency, safety, and cost-effectiveness. An innovative thinker with practical supply chain experience, Michael crafts solutions that help the industry adapt and thrive amid the digital revolution.