Pioneering the path to green steel: Challenges, innovations, and the road ahead
Two recent podcast episodes featuring Hatch experts Randy McMeekin, Ge Sa, Ian Cameron, and Chris Walker, shed light on the critical role of innovation, collaboration, and technological transformation in decarbonizing the steel sector. From green steel projects to advancements in electric ironmaking, these discussions highlight the challenges and opportunities in creating a more sustainable future for steel production.
The urgent need for decarbonization
The steel industry is no stranger to incremental improvements in efficiency, but traditional evolutionary advancements are not enough to address the urgency of climate change. The demand for a drastic reduction in CO2 emissions necessitates a revolutionary approach to steel production. This revolution will require significant capital investments, particularly in regions like North America and Europe, where green steel projects are poised to take off. However, the scale of these projects—often covering hydrogen production, ironmaking, steelmaking, and carbon capture—is unprecedented in recent years, presenting formidable challenges.
These large-scale integrated projects are vital to decarbonization, but their complexity requires technical innovation and new models of project execution. It’s vital to tackle these challenges by focusing on capital efficiency and leveraging digital project delivery tools. By utilizing digital technologies, leaders can improve the efficiency and transparency of project management, ensuring that green steel projects can be executed on time and within budget. This is essential in an industry where projects of this magnitude are rare, and any delays or cost overruns could derail decarbonization efforts.
Greenfield vs. Brownfield: The unique challenges of each
A key consideration in these projects is whether they involve greenfield or brownfield developments. Greenfield projects, which involve the construction of new facilities, generally come with fewer constraints. However, they require significant upfront capital and pose risks in terms of project feasibility and execution. Brownfield projects, on the other hand, involve the transformation of existing operational plants. While these projects can be more cost-effective in certain cases, they present unique challenges, such as ensuring continuous operation during construction and mitigating safety concerns.
Both types of projects require extensive collaboration across the value chain. Early involvement of technology suppliers, contractors, and local communities is essential for identifying potential risks and developing mitigation strategies. The success of green steel projects depends on cutting-edge technologies and on the strength of partnerships. This collaborative approach reduces risks and improves the likelihood of meeting environmental sustainability targets while maintaining operational efficiency and financial sustainability of the business.
Collaboration and de-risking: Lessons from the non-ferrous industry
Drawing parallels with the non-ferrous metals industry, leaders should be focused on the importance of a collaborative, rather than purely contractual, approach to project execution. The non-ferrous industry successfully eliminated sulfur dioxide (SO2) emissions through close cooperation among stakeholders, and the same principles can be applied to decarbonizing steel. By forming teams early and involving all stakeholders in the project life cycle—from technology providers to end-users—the industry can better navigate the complexities of green steel projects.
This collaborative mindset is particularly crucial in de-risking projects. Large-scale decarbonization efforts, such as those required in the steel industry, involve numerous uncertainties, including regulatory changes, technological advancements, and fluctuating market conditions. Early engagement with all parties allows for more flexible and adaptive project management, ensuring that any issues can be addressed proactively rather than reactively. This approach can lead to better outcomes, as it fosters trust and transparency among all stakeholders, driving innovation and problem-solving in real time.
Electric ironmaking: A key solution in the decarbonization toolkit
One of the most promising advancements for decarbonizing steel production is DRI production followed by electric ironmaking, specifically using an electric smelting furnace (ESF). ESFs are a significant step towards reducing the steel industry's dependency on fossil fuels. Although blast furnaces are established and highly efficient methods, they rely heavily on coal both as a reducing agent and as an energy source for melting to produce molten iron and slag. In contrast, ESFs provide a cleaner option by using electricity for melting and separating iron from slag. This technology is already mature and standard for processing raw materials with high impurities, resulting in large amounts of slag, making it suitable for refining lower-grade ores.
The history of electric furnace technology dates to the late 19th century, with commercial applications emerging in the early 20th century. Hatch has been at the forefront of advancing this technology, particularly in the processing of nickel, platinum group metals, laterite ores, and unique applications of electric ironmaking from non-typical iron ores. The continuous reduction iron steel process (CRISP), developed by Hatch, is one such innovation aimed at optimizing electric ironmaking for future production needs.
But blast furnaces, refined over decades for optimal thermal and chemical efficiency, are not easily replaced. Driven by the need for CO2 reduction and advancements in ESF technology, the DRP-ESF pathway currently stands as the most cost-efficient and technologically sophisticated solution available. It offers remarkable flexibility regarding the materials that can be processed and can seamlessly integrate with hydrogen-based reduction and fluid bed reduction processes as they evolve.
High-temperature molten oxide electrolysis is another potential replacement. While promising, this option is still in development and requires further work to reach commercial viability at the scale required for steelmaking.
The future of steel: Balancing innovation with practicality
The road to decarbonizing the steel industry is long, but experts are optimistic about the industry’s ability to meet the challenge. The key lies in balancing cutting-edge innovation with practical, scalable solutions. For example, while hydrogen-based reduction and high-temperature electrolysis offer exciting possibilities, they must be integrated into the broader steelmaking ecosystem in a way that makes economic sense. This includes ensuring that the infrastructure for hydrogen production and distribution is in place and that the costs of these technologies can be brought down through economies of scale.
In the meantime, incremental improvements in electric smelting furnace technology and carbon capture solutions will play a critical role in reducing emissions in the short term. The steel industry has a long history of adapting to new technologies, and the transition to electric ironmaking is just the latest chapter in this ongoing evolution.
A collaborative effort toward sustainability
The path to a decarbonized steel industry is a complex, multifaceted journey that requires the combined efforts of technology innovators, project managers, and stakeholders across the value chain. By embracing new technologies like electric smelting furnaces and adopting a collaborative approach to project execution, the industry can make meaningful strides toward reducing its carbon footprint. Lessons learned from other sectors offer valuable insights into how to de-risk projects and drive innovation through cooperation.
Hatch is looking toward the future of steel, where success lies in the industry’s ability to rethink traditional approaches, embrace new technologies, and work together to achieve a common goal: a sustainable, decarbonized future. The challenges are significant, but with the right strategies in place, the steel industry is well-positioned to lead the way in the global fight against climate change. Contact us to find out more about ways we’re partnering with our clients to decarbonize the steel industry and listen to our podcast series here.
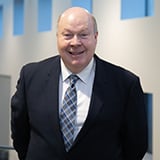
Ian Cameron
Principal Engineer, Ferrous Metallurgy, Pyrometallurgy
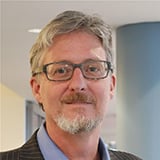
Chris Walker
Global Director of Electric Furnace, Technologies
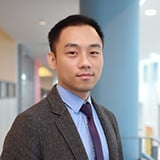
Ge Sa
Engineer - Specialist Process, Pyrometallurgy