Transitioning from gas guzzlers to electron expenders: can traditional car manufacturers catch up with Tesla’s market cap?
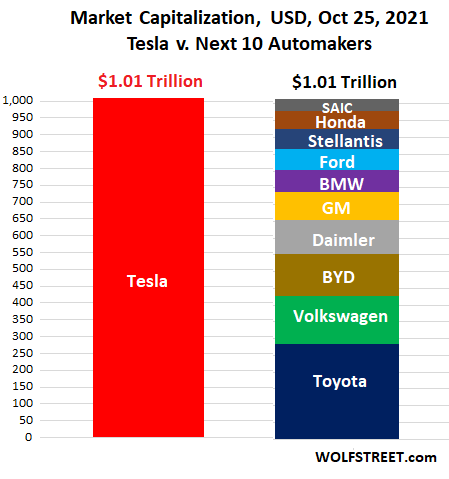
How and why did Tesla grow so quickly?
One of the main reasons is the market’s perception that legacy automakers are gripped by institutional inertia, struggling to transition from a horse-power driven manufacturing, sales, engineering, and retail sales supplier with traditional revenue streams, to electric technology companies. The momentous challenge of this transition demands dramatic changes to the culture of the companies undergoing this transformation. Based on capitalizations, it seems that the market thinks this change is unlikely… without help.
For over a century, automotive companies have competed against each other largely by focusing marketing and engineering resources on the horsepower, torque, and “muscle” of their products, which at their core are finely tuned masterpieces of traditional combustion and mechanical engineering. Engineers and technologists from the best universities and colleges would be hired by the manufacturer’s research and development labs to develop the next version of the 4-, 6-, or 8-cylinder engines to develop the latest and greatest models, with minimal iteration from one generation of product to the next.
Most automotive companies tend to be locked into manufacturing facilities and labor agreements tied to their existing business models. They source the cheapest materials that can withstand the greatest combustion temperatures while reducing mass production costs and marketing their products’ specific advantages over the competition to their traditional customer bases. Some consumers look for more horsepower, others for fuel efficiency, and still others for a comfortable box on wheels to get them safely from home to work, and back again.
The challenge faced by legacy automotive manufacturers is to leverage traditional automotive knowledge, manufacturing facilities, labor, finely tuned work processes, and existing customer base while making a drastic shift of what they build and sell. This includes everything from the supply chain needing to source battery components, to a shift from largely mechanical to electrical engineers, and changing customer expectations concerning emissions and embedded technology. Oh, and don’t forget the aftermarket services teams that may not have yet realized that an electric vehicle with 5% of the moving parts as a traditional gas-powered car, won’t need to be fixed nearly as often, thus having a profound effect on their business model.
New knowledge required
Successfully transitioning to a top tier EV provider, beyond partnering with companies such as Apple, Samsung, Panasonic, and Hitachi, will require traditional automobile manufacturers to develop and learn skills beyond legacy vehicle engineering. Already, several automotive manufacturers are finding they need to be more involved in supply chain management if they are to control costs and adequately mitigate risks.
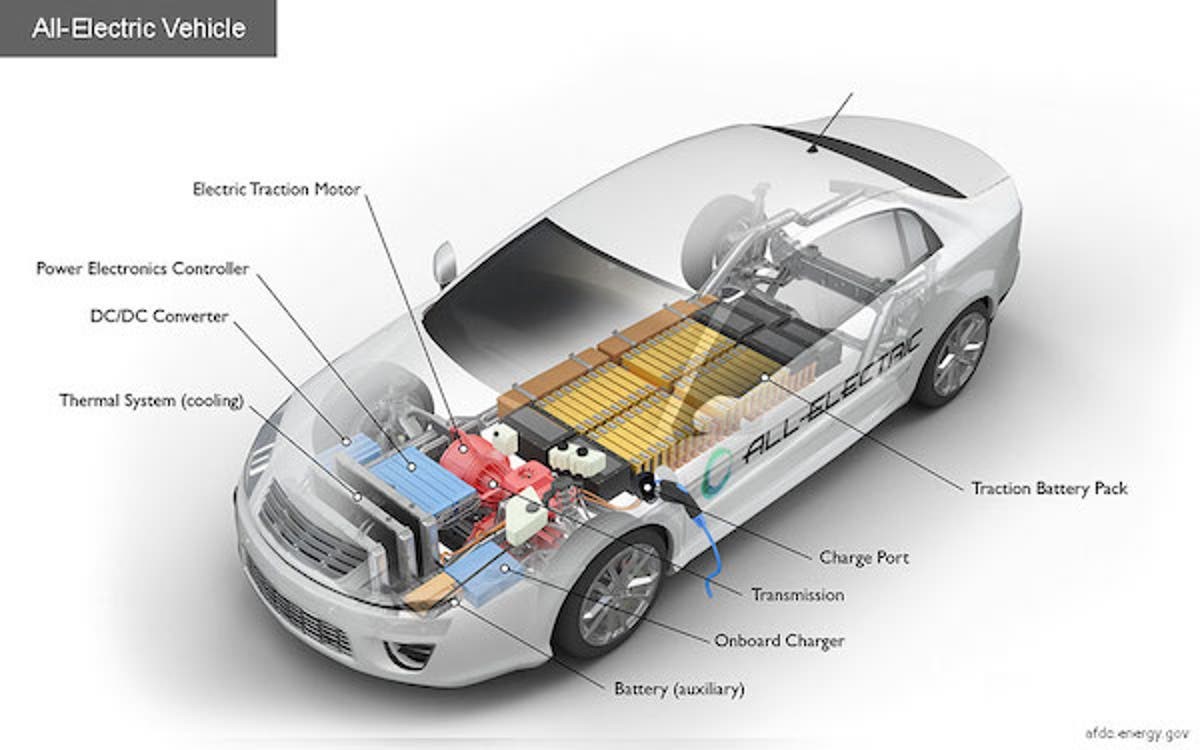
Automotive original equipment manufacturers (OEMs) will need to leverage existing experts in battery chemistries, raw material market awareness, integrated EV drivetrain systems, and energy management systems as never before to improve their competitive advantage.
Legacy dealerships and maintenance personnel will need to learn new skills and be trained to perform EV diagnostics and maintenance.
Moving down the supply chain, automobile manufacturers will need to ensure there are sufficient compatible chargers in the markets they wish to sell, whether for customers parking at a single-family home, multi-unit condo, work, destination, or on-street parking, and that enough capacity exists to support rapid charging for longer road trips. In some markets, OEM’s may need to partner or build their own charging networks to ensure sufficient coverage. Automotive suppliers will need support for running power system flow analysis to determine if the local utility can supply the power needed, and if any demand side management or energy storage might be appropriate to protect the grid from peak loads.
Moving up the supply chain, carmakers will need to form partnerships with battery manufacturers and mines for critical chemical elements such as lithium, graphite, cobalt, and nickel. Some may even choose to develop their own batteries, rather than depending on existing and new OEMs. They may have to choose between multiple battery chemistries and adjust the chemistries to local climate and market conditions. Significant research would have to be done on the supply chain availability for battery raw materials of various compositions.
Some manufactures are already purchasing and investing in mining operations to secure sufficient raw materials for the increase in demand expected in the next five to ten years. However, top-tier automotive manufacturers know very little about nickel reduction furnaces, ball mills, sulfide smelting, leaching, cobalt electrolysis, or graphite comminution and reverse or froth flotation. They would also need to understand the steps and schedule expectations to transform a qualified mineral ore discovery to an operating mine at full production. As for the sourcing of rare earth minerals, there are geopolitically sensitive regions they may wish to avoid.
Help is available
To jumpstart their transition, traditional automotive manufacturers should work with engineering partners that are technology agnostic to avoid being pulled in one direction or another. They should seek engineering partners with the electric power, infrastructure, and minerals extractive development experience they need. Partners that:
- Have experience across the energy sector for the power needs; the infrastructure sector for the overall system management and integration needs; and the mining sector to understand what is needed to sustainably secure the upstream supply chain
- Actively integrate batteries into power systems and understand the impact of EV growth on grid stability to identify partnering opportunities with utilities, municipalities, and infrastructure investors
- Thrive on innovation within power generation, distribution, and local supply and associated electrical infrastructure power modeling, protection systems, and bi-directional control systems from a grid level down to the vehicle energy management system needed to maximize battery usefulness while not degrading expected life
- Challenge the status quo designing end-to-end transportation systems, creating equipment specifications for electrified transportation infrastructure, and have experience with light, medium, and heavy-duty vehicle electrification and charging infrastructure
- Have been developing and designing raw mineral and metal extraction and processing plants for decades to ensure the entire supply chain can meet the assembly plant supply needs sustainably at what is appearing to be an exponentially increasing rate
Tesla has managed to develop most of this knowledge under the radar over the years. When traditional manufacturers demonstrate that they can also meet these challenges, or at least have solid plans in place to address them, it is likely that they will be rewarded with increased market capitalization. After all, once the initial pilot models move into full production and the technical issues are under control, what good is a great electric vehicle design if the upstream supply chain required to meet demand lacks the availability of critical raw materials, or if there is insufficient power and charging infrastructure available?
With nearly 19 years of corporate existence, and only 14 years since its first vehicle (the Roadster) went into limited serial production, Tesla has been quick to grow to the market capitalization it has today. But as efficient as that may seem, traditional automakers don’t have the luxury of even half that time to develop their expertise in all the areas required to support an EV ecosystem. Automotive companies should be visibly reaching out to the right engineering consultancies to leverage the applicable pre-existing experience. Reach out to our team at Hatch today to accelerate the curve!