Project delivery strategies during COVID-19: Kenmare Resources as an African case study
We had a unique opportunity to sit down with Ben Baxter, Chief Operating Officer at Kenmare, to talk about successfully delivering the WCP B project during COVID-19.
Hatch: Ben, thank you for joining us! Kenmare was faced with a unique and unexpected challenge when the global pandemic reached Mozambique at a critical time during the WCP B relocation project. Tell us about what that meant for the team.
Ben: Our team had to deliver a prompt response to the escalating COVID-19 risk on-site to make sure that we delivered on our highest priority—safety in the workplace—as well as to make sure that we were giving ourselves the best chance to deliver this project on time. We did this through the implementation of additional sanitation stations and social distancing measures; by introducing mandatory travel isolations; and by building a testing facility at the mine. We also got early agreement from our main contractors and Hatch, our EPCM provider, to have their site teams present for the duration of the contract, which was a key part of our success.
Hatch: What were some of the challenges that you faced during this time?
Ben: First, we had to rapidly adapt to legislation that was changing as we were going along. Mozambique introduced a state of emergency and there were progressive lockdowns across the world, particularly in South Africa, where we had a lot of fabrication taking place. This led to restrictions on the movement of people and goods. In the first half of 2020, we experienced delayed fabrications and the relocation of contracts to countries in other parts of the world that were not in lockdown. In the second half of the year, the main challenge was really to get people into Mozambique, both the installation contractors and the move team.
Hatch: How did you adapt to address these challenges?
Ben: We had to be dynamic and we had to follow an integrated project management approach. And, by integrated, I mean the integration of our owner’s team, Hatch, and our contractors. Early and frequent communication was key and having a detailed understanding of schedule compliance was critical, with multiple critical workstreams being assessed at any one time. The buy-in of the owner’s team, the EPCM provider, and the contractors was essential, and we found that we had a “can-do” attitude across all three of those groups. That allowed us to define alternative suppliers and/or sub-contractors early, if they were required, and to refocus the project towards more in-country resources. We even saw that contractors supported each other for schedule compliance. They would re-allocate scope between them according to the resources that were available on site at any one time. And, because of Kenmare’s country management experience, we were able to facilitate their work permits and visas as efficiently as possible.
Hatch: How did an integrated approach help achieve schedule compliance?
Ben: The agility of the teams created innovations and led to the development of the “HMC on time” plan, which was a modification of the original project scope to ensure that heavy mineral concentrate (HMC) would be delivered by Q3 2020. That achievement was essential for the business to get back into production and it meant that we had to mitigate some areas where scope could not be completed on time. Inevitably, COVID-19 brought change, extensions of time, and added costs, but what we realized early was that those costs were outweighed by getting WCP B back into production quickly.
Hatch: What would you say were the key success factors that contributed to the delivery of this project?
Ben: There were many success factors to this project, but the main success was around strong relationships. Our project team became extremely well integrated with the operations team at Moma. We saw that there were fantastic relationships with our EPCM team, particularly personnel that had been with us throughout several previous projects over many years. The dedication of the contractor group was also fantastic—they worked as partners. Every contractor went the extra mile.
Hatch: What do you think helped build those strong relationships? And what were the benefits?
Ben: Those relationships were really built around a good project management system and controls. We had a very prompt understanding of schedule, costs, and risks, and our governance structure was efficient. It allowed the project team to meet the executive committee on a weekly basis, which meant that decisions were made quickly. We were able to give the project team direction without delay. We were also successful because of the time that we spent developing our contracts at the beginning. Those contracts turned out to be very useful when the inevitable claims from COVID-19 and the extensions of time came in. We were able to have open and fair conversations with contractors, and that meant that we had very strong professional relationships, benefiting both sides. The last benefit was the decoupling of the project’s non-mission critical components. This allowed the project team to focus in on what was important and, when we had to change scope to focus on the “HMC on time” project, the team knew what they had to do.
Hatch: Thank you, Ben—any final thoughts?
Ben: This project has been delivered and HMC production commenced on October 25, 2020, as per the plan. In Q4 of last year, we ramped up WCP B back to its normal production rates. I’d like to say a massive congratulations and thank you to our owner’s team, Hatch, and all of our contractors who delivered this move under truly dynamic circumstances.
Find out more!
Listen to Ben present this topic at The Canada-Africa Chamber of Business 22nd Annual African Mining Breakfast & MineAfrica’s 19th Annual Investing in African Mining Seminar. Click here to watch the recording!
To read more about the WCP B relocation project, click here.
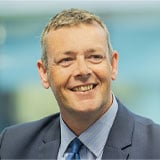
Ben Baxter
Chief Operating Officer, Kenmare Resources
Ben Baxter has spent twenty-five years in the mineral sands industry joining Kenmare Resources plc in 2015 as Chief Operations Officer. He was previously employed by Rio Tinto at RBM in South Africa and QMM in Madagascar where he held a broad range of geological and mine planning roles, was Mineral Separation Plant Manager and Mining Manager, followed by QMM’s General Manager of Operations and RBM’s General Manager of Mining. At Kenmare, Ben is responsible for all aspects of operations and project development and has been a key part of the development of the Moma mine towards a strategy of delivering 1.2 Mt of ilmenite production per annum on a sustainable basis. Ben holds a B.Sc. (Hons.) in Applied Geology from the University of Leicester, UK and an M.Sc. in Mining Geology from the Camborne School of Mines, UK.