Building a resilient supply chain: lessons learned from a time of crisis
A supply chain is a system of people, processes, and resources involved in supplying products or services to a consumer.
The majority of us are fortunate enough not to have ever noticed any (at least long-term) difficulties or shortages when it comes to supply. In fact, I’d say it’s safe to argue that it’s a business sector that typically gets taken for granted unless you’re in a time of crisis. If we look at the recent coronavirus pandemic as a broader example, COVID-19 has presented a unique “perfect storm”: we’ve all seen images of cargo planes shipping supplies to support front-line workers around the world. Yet we’ve also all seen shortages in PPE and hand sanitizer. We’ve witnessed empty shelves at our local grocery stores. This is a basic supply chain. In our industry sectors, the same type of product and service chain occurs with equipment, supplies, and services, which our clients use in their operations.
When crisis hits
Enter a crisis. Borders close. Traditional traffic and operations are restricted. Manufacturers are working on skeleton staff. Production lines are paused. Material deliveries are delayed. We’re seeing the effects first-hand and it’s making us reevaluate how we all operate our businesses. From a supply chain perspective, we need to diversify our supply source and become more resilient. This is where we start to examine the concept of reverse globalization.
Think globally, act locally
Cost efficiency is always at the forefront of running a business. Organizations want to maximize on profit while operating on the lowest costs. In this regard, globalization has had–and has–many benefits. Lower input and product costs, for instance. The problem is, when you encounter a crisis, a hard import stop can follow. And then what?
There’s a lot of talk about domestic circuit supply and localizing production. Of course, it’s easier said than done. It’s not possible to build an entire industry in your backyard. Nor is it cost-effective. But thinking about localization, the risks in our current systems, strategic sourcing, and back-up options is a step in the right direction. We’ve never had to think about dual supply bases or back-ups, and as a result we’ve become victims of our own doing. We now know how critical supply chain resiliency is.
Wake-up call
Wake-up call
What is supply resiliency and why does it matter? We need to be prepared for unexpected disruptions, agile in our response to change, and able to recover quickly. There’s no sure way to overcome high-impact, low-probability events, but the secret is knowing how to cope. Having a strategy. Holding extra inventory. Diversification of supply base geographically. Real-time visibility of the complete supply chain including sub-tiered suppliers and contractors. Stratification and cultivation of supplier relationships. Alternatives and back-up options. Paying attention to greener options. Having back-up processes in place. Flexibility to withstand disruption. Mitigation of risk. Communication. These are the things we need to start paying attention to. Whether you’re a mid-tier organization or a small business, the level of risk is the same. Some companies might have a stronger balance sheet. Some might be more agile. The challenge? Equal. This isn’t about making drastic changes to how you manage your operations (though in some cases those might be required too). This is about making gradual changes in order to minimize impact. And yes, you might have to spend a little bit more at the onset, but it’s worth it in the long run. Navigating a new normal Everyone is part of a supply chain. You participate in a supply chain by going to a grocery store. In a larger scope, perhaps you need to deliver a piece of very expensive equipment to a specific site. The process itself, as well as its risks, are amplified during a crisis. What the present pandemic has demonstrated is an inherent need for preparedness along with a real push for the application of technology, automation, and digitalization. Organizations require real-time monitoring–from production to delivery and distribution. It’s critical to have visibility on your inventory. Some industries are exceptionally advanced in their digital capabilities, while others haven’t quite reached the mark yet. Further to digitalization, the human element is just as important. This is where supply chain relationship management comes into play. At Hatch, as a solutions provider, we know suppliers and have experience in both the advisory/consulting space, while also having our “boots on the ground” in operations. We have a global network of knowledge and resources. This, coupled with digitalized systems, is what highlights efficient business continuity. Navigating a new normal means there is no normal, and there are many opportunities within that awareness. There are many unknowns. But what we do know is there’s now a sense of urgency. We know we can’t ignore supply chain resiliency. We know we need a combination of global sourcing along with local reserve options to strengthen resilience while remaining cost-competitive. We know the time is now. Do you have your back-up solutions in place? What does your supply resiliency look like? |
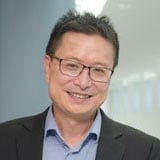
John Chen
Global Director, Procurement
John is a global director for procurement at Hatch with over 30 years of experience in procurement and contract management at both the project and functional levels. John’s project expertise covers mining and metals, energy and, infrastructure. John is a strong advocate of delivering procurement value through early engagement, risk mitigation, proactive collaboration and continuous improvement.