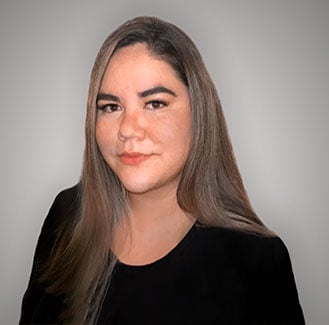
Siobhan Dooley
Control and Automation Engineer, Mining and Metals
Equipped with a bachelor’s degree in chemical engineering from Queen’s University, Siobhan began her career with Hatch eight years ago. Captivated by an article about Hatch’s tireless pursuit for a better world, Siobhan knew she had to join the team. Determined to make a difference in the industry, Siobhan is always willing to tackle the tough, whether it’s through implementing a mine-integrated online management tool to increase productivity or managing the installation of 1,200 meters of radiating cable underground in a day and a half. Whether on-site or in-office, Siobhan brings her full self to work by bringing her Indigenous traditions to site. Most recently, Siobhan participated in a seal skin mitten-making workshop with her colleagues on the Voisey’s Bay mine project.
When not on-site, Siobhan enjoys beading, visiting family, and traveling.
What does positive change mean to you?
“Positive change means two things to me—embracing new technological advances in the industry and ensuring that Indigenous groups are consulted on new mining developments, which historically was not the case.
The systems we’re implementing at Voisey’s Bay are new to the world of underground mining, and it’s been exciting to be involved in the implementation of the systems on-site. Couple that with the fact that the site is dedicated to hiring employees and contractors who hail from the local Indigenous communities, it’s been a great project to grow my professional capabilities.”
What do you think are the toughest challenges facing your clients?
“Ensuring the appropriate resources are in place to properly implement and deliver systems has been one of the bigger challenges I’ve come across. Having the right resources and the quantity of resources in place will ensure that a project is delivered both on time and within budget.”
What are you most proud of?
“I was one of the leads supporting the implementation of a client’s development operational management system on site, training mining operators to use a smartphone to track their tasks and delays. This was a great learning experience for me as it was one of the first tasks I was entrusted with to take lead on. Since then I have moved on to other on-site responsibilities that continue to develop my capabilities.”
What do you like most about working at Hatch? How do you think the Hatch culture is different from other companies?
“The options are endless. I’ve had the opportunity to work on a variety of projects from mine surface facilities support to the management of a solar park facility. Hatch’s culture also fosters a family-type atmosphere amongst a project team, which is something that I appreciate and value.”