Minerai de fer: La transformation de la décarbonisation
L’industrie a fait de grands progrès dans la réduction des émissions de portée 1 (directes) et de portée 2 (indirectes) provenant des ressources qu’elle contrôle ou utilise, comme les véhicules, l’électricité, le chauffage et la climatisation. Toutefois, elle accuse toujours un retard en ce qui concerne les émissions de portée 3, qui comprennent toutes les autres émissions indirectes, en amont et en aval, qui se produisent dans la chaîne de valeur.
Il n’existe pas de solution universelle pour relever les défis liés à la production de minerai de fer et d’acier à faible teneur en carbone. L’industrie sidérurgique vit actuellement un changement majeur en ce qui concerne la technologie. La question est la suivante : qu’adviendra-t-il de l’industrie lorsque la technologie dominante d’élaboration de l’acier ne comprendra plus de hauts fourneaux à forte intensité en carbone? Les stratégies varient en fonction de divers facteurs, notamment l’emplacement, le type de minerai et les sources d’énergie disponibles. Toutefois, la nécessité pour l’industrie d’innover et de s’adapter continuellement est l’une des stratégies les plus mentionnées.
Approche de l’Amérique du Nord
La région nord-américaine a produit environ 104 millions de tonnes de minerai de fer en 2023, dont 60 millions de tonnes provenant du Canada et 44 millions de tonnes des États-Unis. Le minerai en Amérique du Nord, principalement l’hématite et la magnétite, est pauvre, mais il réagit bien à l’enrichissement, un procédé qui améliore la qualité du minerai de fer en éliminant les impuretés.
Le principal avantage des États-Unis est la capacité de libération de leur minerai, ce qui signifie qu’il peut être facilement séparé pendant le traitement, mais qu’il doit tout de même être enrichi.
Les procédés d’enrichissement produisent du minerai riche qui peut être utilisé comme charge d’alimentation, habituellement sous forme de boulettes ou de briquettes, lors du procédé traditionnel de réduction directe (RD). Il en résulte du fer et de l’acier avec des émissions de carbone bien plus faibles. Toutefois, ce procédé nécessite d’importantes ressources, notamment en eau, en énergie et en produits consommables, et génère en plus des résidus à gérer. Le rendement moyen de récupération est généralement de 78 à 82 % de la teneur totale en métaux ferreux, tandis qu’une partie du fer plus pur est perdue dans les résidus miniers.
Au Canada, le minerai de fer de grande pureté a été reconnu comme un minerai critique, particulièrement dans la fosse du Labrador. Cette reconnaissance a favorisé la collaboration entre les exploitants, le gouvernement et d’autres intervenants pour soutenir la décarbonisation des industries du minerai de fer et de l’acier. Le minerai de fer de haute qualité de la fosse du Labrador en fait un candidat idéal pour produire du minerai de fer de qualité RD, essentiel à une production d’acier plus écologique à l’aide des technologies existantes.
Approche de l’Amérique du Sud
En Amérique du Sud, l’industrie brésilienne du minerai de fer est confrontée à des défis semblables à ceux d’autres régions, notamment la nécessité de réduire les émissions et d’améliorer l’efficacité. Le gisement du Brésil est riche en métaux ferreux et contient très peu d’impuretés nuisibles. Il s’agit d’un grand avantage économique pour la production à faible coût de minerai de fer et d’acier. En 2024, la production totale de fer du Brésil s’élevait à environ 440 millions de tonnes. Toutefois, les boulettes de qualité RD, très recherchées pour leur utilisation dans l’élaboration de l’acier écoresponsable, ne représentaient que 10 à 15 % de cette production.
Par conséquent, le Brésil se concentre de plus en plus sur la production de boulettes de qualité RD supérieure pour exploiter de nouveaux marchés et stimuler les exportations en ajoutant une capacité d’enrichissement à mesure que la teneur et la qualité du minerai brut diminuent de manière générale. Ce changement vise à répondre à la demande croissante de ces boulettes et à tirer parti de leurs avantages économiques et environnementaux.
Secteur du minerai de fer en Australie
L’Australie est le plus grand exportateur de minerai de fer au monde, exportant environ un milliard de tonnes par année, principalement de la goethite et de l’hématite provenant de la région de Pilbara. Le minerai est riche en gangue (alumine et silice) et convient parfaitement aux hauts fourneaux. En raison de la structure cristalline unique du minerai, il n’existe actuellement aucune voie d’enrichissement commercialement viable pour réduire suffisamment la gangue pour les marchés ou les procédés du minerai riche.
Certaines des plus grandes mines de minerai de fer au monde se trouvent dans la région de Pilbara. Elle représente plus de 50 % de la production mondiale. Les tracés d’expédition de l’Australie à l’Asie sont parfaitement adaptés pour accueillir toute la production de hauts fourneaux entre les continents. Les producteurs australiens de minerai de fer travaillent en étroite collaboration avec les producteurs d’acier de l’Asie pour soutenir la transition vers une technologie plus verte et sans carbone. Évidemment, comme pour tout producteur, il est important de suivre le rythme du marché. Les producteurs de Pilbara en sont très conscients et s’efforcent de manière proactive de soutenir la transition vers une technologie sans carbone. Il s’agit notamment d’investir dans l’aménagement d’un four de fusion électrique (FFR) et d’un four de réduction directe (FRD) pour le minerai à teneur supérieure en gangue de Pilbara.
Fait intéressant, l’Australie possède de vastes réserves de magnétite, mais la goethite est si facile à traiter et il existe un marché si important pour elle, qu’il n’est pas nécessaire d’investir dans l’agrandissement de la magnétite. Cela dit, la faible quantité de magnétite extraite, tant pour la consommation locale que pour l’exportation, augmente à mesure que la demande mondiale de boulettes de qualité RD grandit.
Explorer des sources d’énergie de remplacement
D’autres sources d’énergie comme l’huile pyrolytique et les pistolets à plasma sont envisagées pour soutenir une production plus écologique de minerai de fer. Les petits réacteurs modulaires (PRM) sont également perçus comme une source d’énergie potentielle. Malgré la complexité de leur mise en œuvre, les PRM pourraient constituer une source d’énergie fiable et à faible émission de carbone pour l’industrie du minerai de fer.
L’élaboration de nouvelles technologies de procédés et de solutions novatrices est essentielle à l’avenir de l’industrie du minerai de fer. Ces progrès peuvent aider à relever les défis liés à la production de minerai riche et à soutenir la décarbonisation de la chaîne de valeur de l’acier. En investissant dans la recherche et le développement, l’industrie peut trouver de nouvelles façons d’améliorer son efficacité et de réduire son impact environnemental.
Travailler ensemble vers la réussite
La collaboration avec un partenaire comme Hatch peut aider les clients de l’industrie du minerai de fer à réussir en leur offrant des solutions novatrices et durables dans l’ensemble de la chaîne de valeur, des phases de l’extraction et de la valorisation à l’agglomération de minerai. Notre expertise en technologies de pointe, en efficacité opérationnelle et en responsabilité environnementale s’étend sur plus de 60 ans et permet à nos clients de maximiser leur production, de réduire leurs coûts et d’atteindre leurs objectifs de durabilité.
Qu’il s’agisse des procédés d’enrichissement en Amérique du Nord, de l’accent mis par le Brésil sur les boulettes de qualité RD ou de la collaboration de l’Australie avec les producteurs d’acier de l’Asie, l’industrie fait des progrès vers un avenir plus durable. En adoptant des technologies novatrices et des sources d’énergie de remplacement, le secteur du minerai de fer peut continuer à réduire les émissions et à améliorer son efficacité.
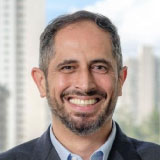
Bruno Vartuli
Senior Metals Consultant Iron & Steel, Project Development
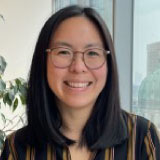
Stefanie Vo
Iron Ore Processing Specialist, Mineral Processing
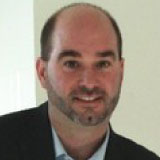
Martin Dionne
Global Commodity Director, Iron Ore & Co, Project Development