Discrete Element Method (DEM) simulation for operational validation of your bulk material production assets
Any bottlenecks result in budget and schedule overruns that ultimately affect a clients’ bottom line. Using discrete element method (DEM) simulation in the early design stages of a facility or project can help avoid these issues and achieve the nominated nameplate capacity of the equipment.
DEM is a software tool that provides accurate visual simulation of how bulk material flows and interacts with equipment, such as transfer chutes, underground production hoists, and run of mine (ROM) ore sizer systems.
Since it is a simulation, the computer-aided engineering opportunities allow more cost-effective concept development and validation than designing a physical model, or onsite modifications of the equipment during commissioning. The versatility of the DEM provides advantages in being able to quantify a wide range of metrics.
For example, clients who require a transfer chute to transport granular material, could use DEM to analyze any number of “what-if” scenarios. They could simulate how fast the material flow would be for a range of flowability characteristics. They could simulate a surge loading effect or plugging event and be able to pinpoint the problem’s initiation location and develop solutions to remedy it.
Image 1: DEM assessment of sticky abrasive ROM copper ore at three capacities and diverter operation to feed either of two receiving conveyors.
This type of troubleshooting capability is invaluable and can be applied to multiple industrial sectors, including mining, minerals processing, and energy with positive results. In mining, for example, DEM simulation can predict the long-term effect that heavy, sharp-edged abrasive iron ore would have on equipment wear life, thus allowing clients to stay on top of maintenance issues.
DEM simulation can also support project startups by applying a “digital” commissioning approach that allows clients to determine and optimize bulk material flow requirements and equipment configurations in a computer-aided engineering (CAE) environment before progressing to fabrication and installation.
There are several reasons why DEM has become a more effective and accepted simulation tool, including:
- DEM software packages – once limited to university research and development departments – are more widely established and available in the public domain.
- Ongoing computer hardware development, particularly graphic processing (GPU) advancements and computational power, allow for ever-increasing high-resolution virtual simulation and increasingly larger particle populations.
- Established acceptance by major client companies of the benefits of DEM in validating bulk materials equipment and design within the engineering phase for large projects. The utilization of DEM by major OEMs in their respective equipment design development is noteworthy.
DEM simulation, which has an established track record in providing clients with innovative, practical solutions for equipment handling bulk granular materials, has a promising future.
Additional benefits are attained when coupled with other CAE software modules, primarily computational fluid dynamics (to simulate the interaction of fluids and granular solids), finite element analysis (for structural analysis under granular solid loading problems), and mechanical multibody systems (to predict equipment behavior interacting with bulk material scenarios). See Image 2.
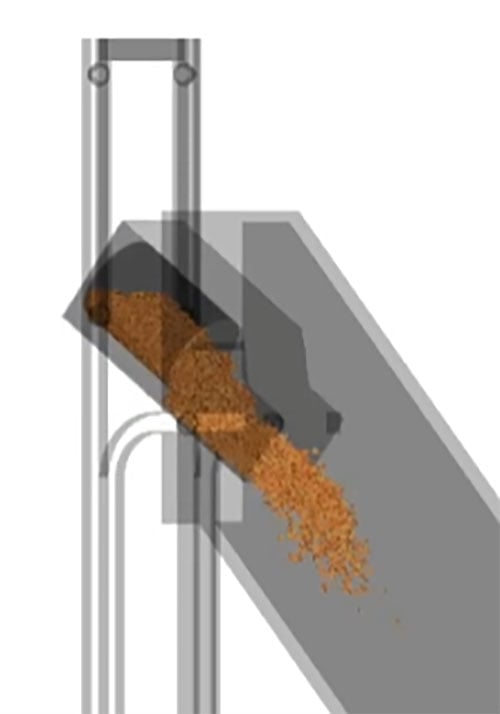
Image 2: Drum lifter discharge motion assessment (coupled DEM and multibody motion simulation, with the drum lifter tipping motion controlled by the guide wheel travel within the profiled tracks).
And there continues to be a myriad of new applications that are transitioning from research and development initiatives to valid industrial opportunities. Examples of these opportunities include complex particle shapes including flexible particles, development of new material contact models and utilization in storage bin engineering, particle breakage modeling with applications in material degradation (refer to Image 3) and comminution, modeling of material flows incorporating heat transfer analysis, or magnetic, electrostatic fields, and assessment of segregation and blending efficiency of particle assemblages.
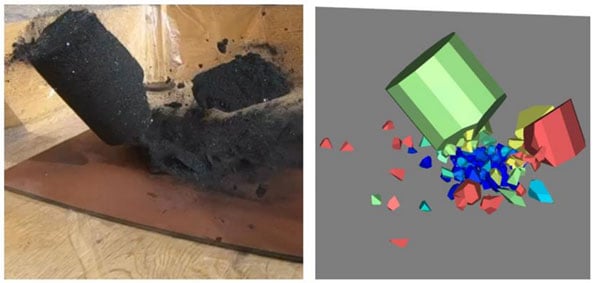
Image 3: Frozen ore degradation calibration and DEM modelling for assessment of BMH equipment
When it comes to simulating the handling and flow of bulk materials, it is fair to say that DEM is a model for success.
See Luke Stone’s blog on advanced simulations to understand seasonal effects on operations that details how frozen material in a grizzly caused blockages and how DEM was used to better understand the operational challenge so the issue could be solved.
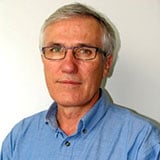
Brian Moore
Bulk Materials Handling subject matter expert, Bulk Materials Handling
Brian is a leader in granular flow performance for bulk materials handling including DEM simulations of transfer chutes, screens and associated BMH equipment. He frequently undertakes troubleshooting investigations of existing materials handling plants and providing plant design recommendations for handling wet and sticky ores.